Behind the lube: testing, refining and proving the concept
Author: NEOL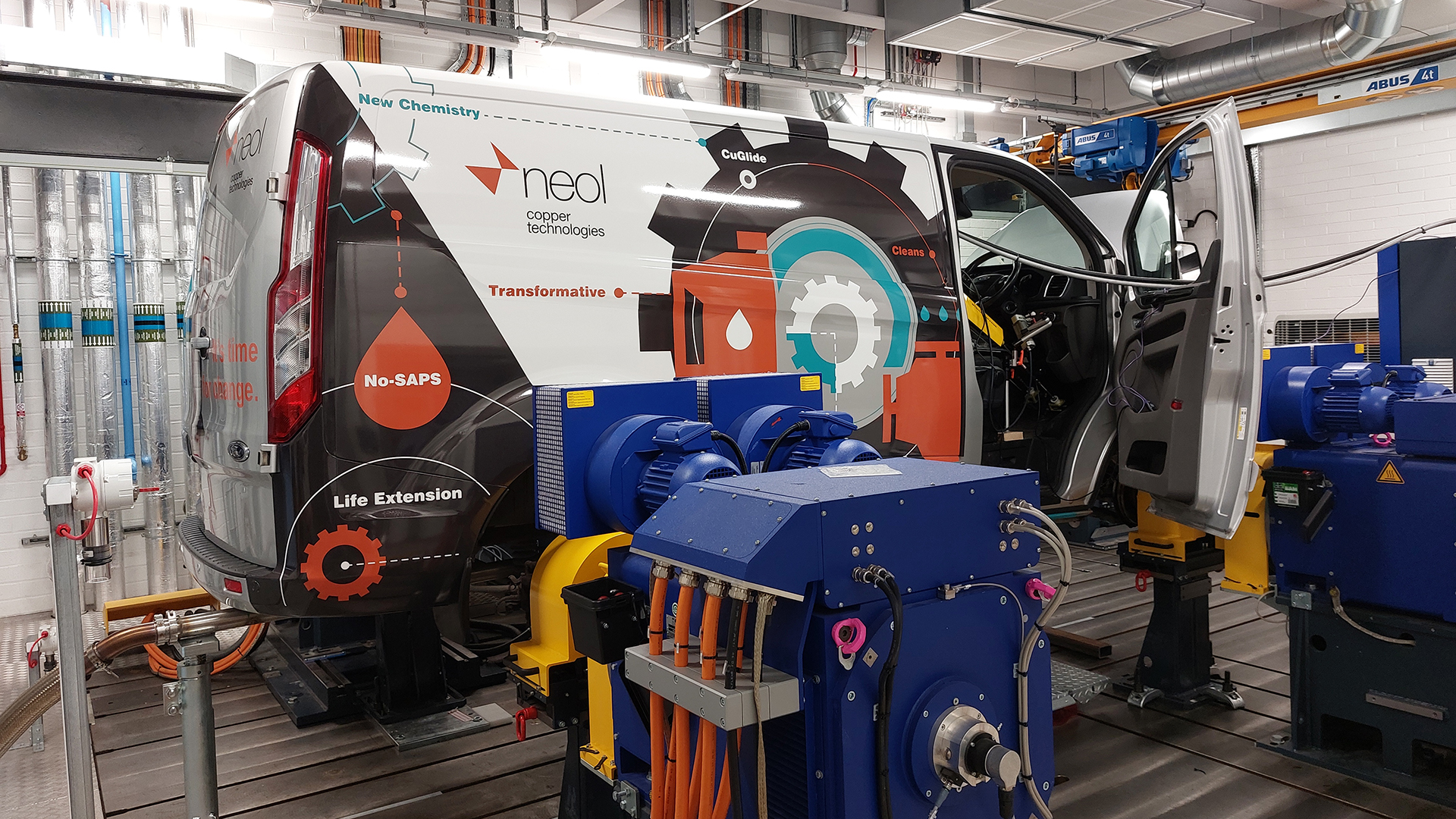
Outside of the lubricants industry, its probably fair to say that not a great deal of thought is given to how a lubricant has been developed, or even which lubricant is used. For the most part, vehicle owners or machine operators will look at what has been approved by the original equipment manufacturer (OEM) – or what their parents and grandparents used – and then carry on using that for the duration.
There is of course a logic to this. The oil or grease must have gone through several tests before being approved and, in many cases, using something unapproved can end up voiding any warranty in place.
The problem, however, is that the high costs and lengthy approval processes unfortunately prohibit any significant breakthroughs in lubricant technology. OEMs and regulatory bodies use tests that are largely based around widely used lubricants already in place, that haven’t seen much change over the last 60 years and, arguably, aren’t nearly as effective or environmentally friendly as they otherwise could be.
The paradox of industry testing
Lubricant testing in the industry typically involves a series of standardised bench tests and field trials, some lasting for multiple years, designed to evaluate a lubricant’s performance under various conditions. These tests assess properties such as wear protection, viscosity stability, piston cleanliness, oxidation and nitration stability, aeration, fuel economy, and corrosion resistance, ensuring that the lubricants meet or exceed the specifications set by OEMs and regulatory bodies.
But many of these tests have been purposefully over-engineered to the point that they no longer apply to real-world conditions. Take the 4-ball test for example. This is a test used to help determine how a lubricant will perform under extreme pressure and the level of wear resistance it provides. Yet, the conditions of tests – namely how the balls move and interact with each other – don’t really represent those seen in actual machine usage.
As such, it doesn’t provide accurate information on how a lubricant will truly perform. In fact, a 2008 research paper written by members of the FZG institute found that both a hydraulic oil and gear oil performed lower on this test that common household liquids such as beer and milk.
There is also a certain irony in the certification requirements from two of the major regulatory bodies. Following the introduction of diesel particulate filters (and more recent petrol particulate filters) – which are designed to reduce the level of harmful exhaust emissions from engines – there has been increasing pressure to reduce SAPS levels in engine oils. This is because the SAPS content can block and poison the filter as it is burnt.
Yet, although the American Petroleum Institute (API) and European Automobile Manufacturers’ Association (ACEA) have certification for low-SAPS lubricants, there is nothing currently available for a no-SAPS alternative. This is because history has suggested that the only way a lubricant can pass these tests is by using SAPS containing technology.
Now that we are able to provide an alternative free of SAPS, there is unfortunately nothing to test it against.
More effective ways to prove a lubricant’s efficacy
None of this is to say that lubricants shouldn’t be thoroughly tested to ensure they are safe for use. They absolutely should. But the tests that are going to give the most useful results are those that determine how a lubricant performs in the real world.
At NEOL, we have focused on testing our CuGlide technology in real-world applications and with laboratory tests that simulate actual operating conditions, to demonstrate the efficacy of our lubricants beyond the traditional benchmarks. This means testing our oils and greases in both new and old engines, under a wide variety of conditions, to prove that they not only protect new machinery, but they also rejuvenate and restore the old.
We have spent decades proving that our technology works and have seen overwhelmingly positive results. And yet, with the current requirements, our lubricants will never be certified, because we are offering an ultra-low TBN, no-SAPS alternative to traditional oils and greases.
We would love to see a future where industry testing and specifications evolve to recognize and accommodate innovation. Until then, however, we will continue to rigorously test our lubricants and demonstrate that it’s possible to achieve superior engine protection, enhanced performance, and environmental sustainability all in one package.
As the industry continues to evolve, we are determined to play a pivotal role in shaping the future of lubricants, offering new solutions to decades-old challenges, and opening new avenues for research and development.
After all, it is time for change.