CuGlide™: a revolutionary approach to combating wear
Author: NEOL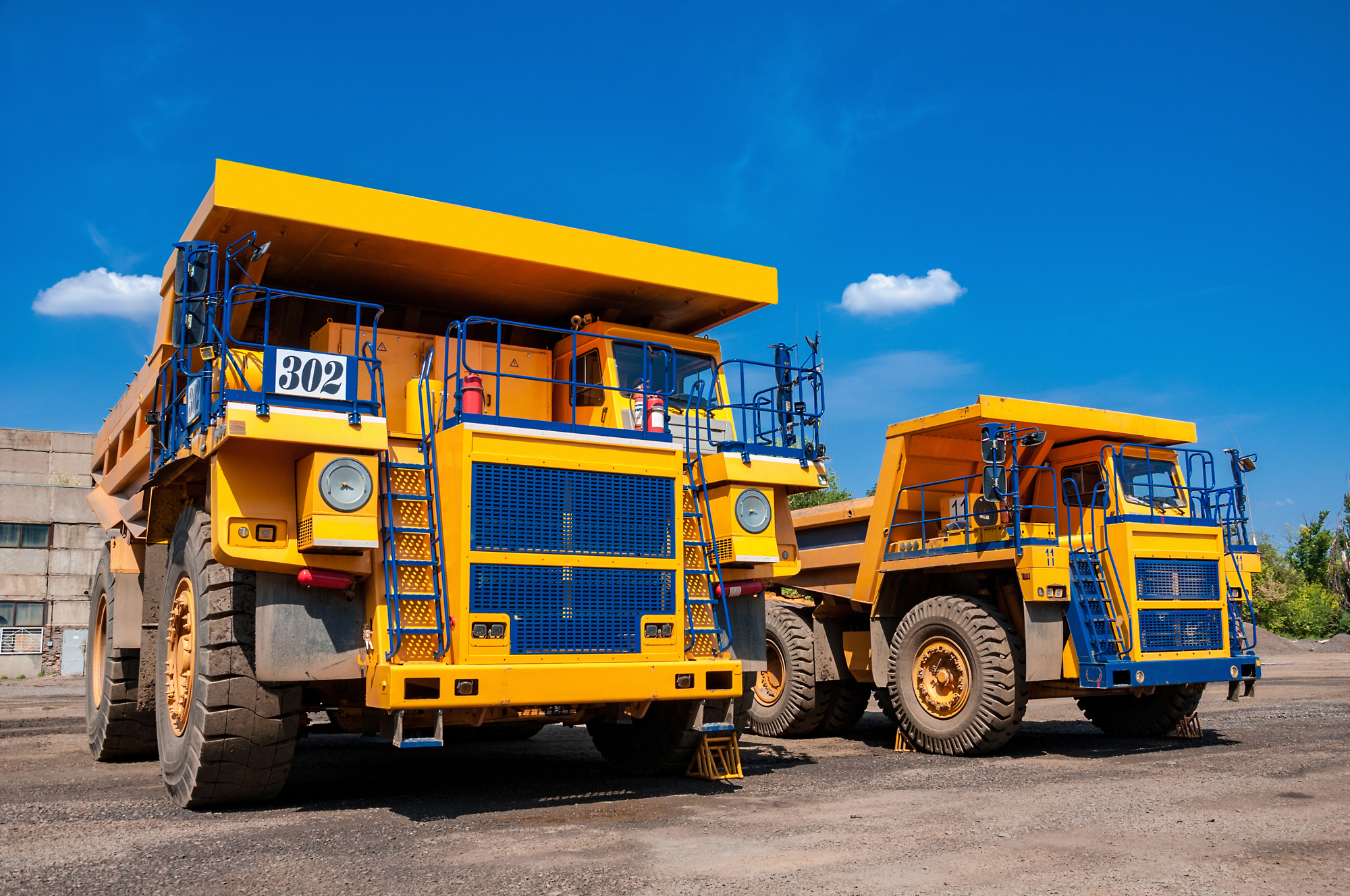
Wear and tear is a challenge that industries and companies have grappled with for centuries. Today, whether it’s fleet owners, machine operators, or railway companies, the gradual wearing down of mechanical parts is an issue that leads to higher operating costs and costly replacements – not to mention the environmental implications that come with the disposal of old machinery.
Yet, for as long as we have had machinery, wear and tear has been accepted as an inevitability. Lubricants have been developed to slow the process, but there has been little done to prevent it in its entirety or to fix the damage it causes.
This is where CuGlide comes in. It is a revolutionary new approach to lubricant technology that not only tackles this age-old problem but does so in an environmentally responsible manner. It marks a significant leap forward in the battle against wear and tear, with the power to prevent many known forms of wear and even restore previously damaged parts.
The science behind CuGlide
CuGlide works by utilising the power of “hydrogen wear” and “the wearlessness effect” phenomena. Though friction is normally viewed as the main cause of wear between two surfaces – i.e., things rub together, and wear happens – when you combine it with the selective transfer of copper ions (the wearlessness effect), friction becomes an evolutionary process, and the erosion of surfaces becomes secondary.
In essence, the exchange of energy and matter at the friction surface allows for ions to be transferred. Metal surfaces connect with each other generating the heat and pressure needed for the particles to separate, thereby creating room for hydrogen to invade the surface, but at the same time allowing copper ions to embed themselves in the iron structure. The copper then comes together to form an ultra-thin film over the machine part, protecting it from wear and healing any existing defects. And, because it is friction that creates this protective film, it can no longer destroy it.
So, CuGlide utilises the power of hydrogen wear. Not to be confused with hydrogen embrittlement, which is where absorbed hydrogen reduces the ductility of a metal, hydrogen wear is a major cause of metal surface deterioration in friction units.
Fortunately, hydrogen wear can be controlled. Instead of preventing it completely, CuGlide technology first allows hydrogen to polish the friction surface, then terminates it with the copper ions which are introduced via a scientifically formulated lubricant to create the protective film. Not only does this create a lubricant with superior protection and restoration qualities, but it also means we can create specific oils and greases completely free from harmful organic phosphates.
CuGlide in action
It’s all well and good to say something has the potential to do incredible things, but without putting it into action it is all just theoretical. So, to prove CuGlide technology can deliver the results we have – and will continue to – put it through numerous real-world and laboratory-controlled tests.
One such test was a trial of our full-synthetic ISO VG 220 industrial gear oil (containing the CuGlide additive) in a well-used Sandvik CG820i gyratory crusher, used for processing up to 4,000 tons per hour in mining operations. The test was broken down into two phases: one consisting of a 1,500-hour pilot test, the other using the industrial gear oil in the crusher for more than 5,000 hours.
By breaking the test into two separate phases, we were able to evaluate the oil’s performance in several different areas, assessing its viscosity, acid control, wear protection, detergency, longevity, and cleaning properties.
The results were exceptional. We found the CuGlide-containing oil to have excellent viscosity control at 40°C and 100°C while also offering thermal and oxidative stability. There was no increase in in-service oil acidity, with the lubricant providing oxidation and corrosion protection, and no degradation in performance.
Additionally, the gear parts exposed to high load, stress, and hot temperatures showed no sign of wear during contact. Oil analysis showed there was no iron, chromium, or nickel detected and analysis of the gear parts themselves proved that previously immoveable remnants and debris had been cleared out – cleaning them and restoring their efficiency.
The end results demonstrated how the oil provided robust protection, detergency, and lubrication. This allowed operators to confidently run their equipment more efficiently while saving on maintenance costs.
In another real-world test, a 500-hour field trial was conducted on CAT 777E haul trucks in an open-cast mining operation. This involved the use of no-SAPS synthetic SAE 10W-40 HDDEO formulation (also containing CuGlide) in three trucks, with each vehicle having accumulated 28,000 to 33,000 hours of service.
Once again, the results were fantastic. Oil analysis revealed minimum wear, efficient removal of lead-containing deposits, and excellent control of oxidation and nitration. The fuel consumption data indicated potential cost savings of up to £99,600 per truck – and the drivers also reported improved vehicle acceleration and speed, which delivered an increase in productivity of 1,000km per month.
A new approach for a greener future
NEOL’s CuGlide technology not only addresses the immediate needs of reducing wear and extending the lifespan of machinery but also aligns with broader environmental goals. By moving away from toxic additives and reducing harmful emissions, we are starting a new movement in the lubricant industry, steering it towards more sustainable practices.
We are committed to continuously proving the efficacy of our lubricants and will continue to share the results of our tests as and when they are completed. In addition to the two case studies mentioned above, we have recently carried out tests using a single-cylinder four-stroke Honda motorcycle, a Sea-Pro T 2.5 outboard motor, a four-stroke Yamaha F4BMHS outboard motor, and a four-stroke Yanmar D27 diesel outboard motor.
The results of all of these showed improved fuel-saving performance, engine performance, no-wear protection, reduced exhaust gas emissions, driver satisfaction, and overall eco-friendliness – the full details of which will be posted on our website and on LinkedIn.
Should your company have interest in partnering with NEOL in a collaborative program of work to evaluate our CuGlide technology for either engine and gear lubricants, greases, or to explore performance with hydrogen fuel or EVs, contact via our website: www.neol.world