NEOL Interviews: Sergei Mamykin
Author: NEOL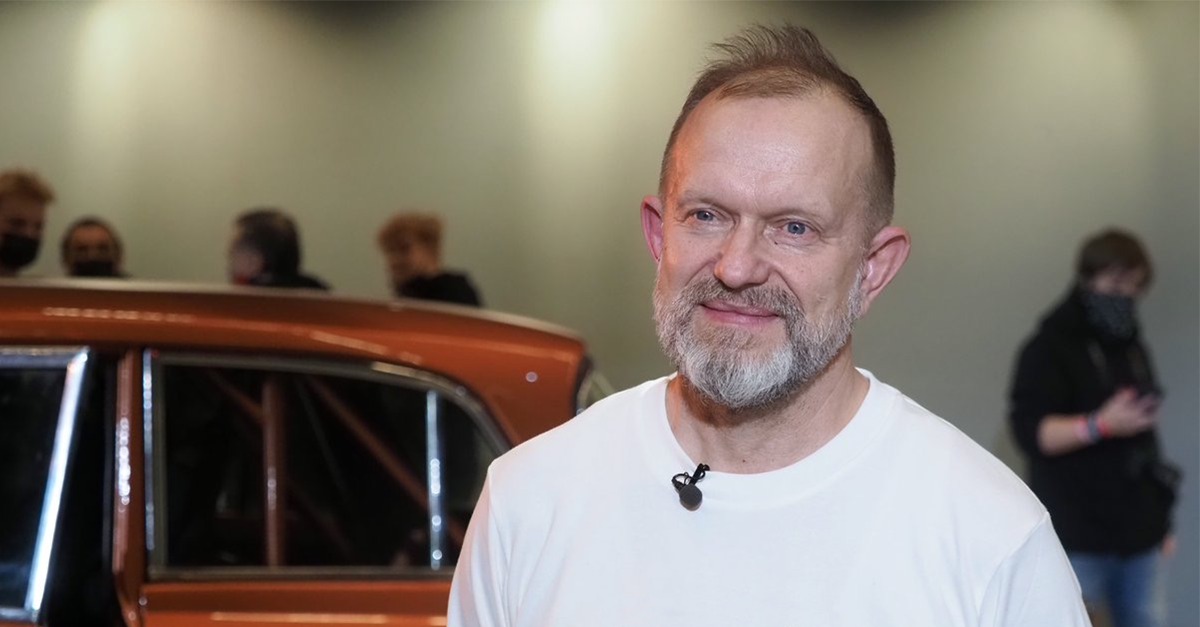
Challenging the status quo is no easy task, particularly when businesses and government officials have built strategies around the very thing you are standing against. Yet, for the vast majority of his career, that is exactly what Dr Sergei Mamykin has been doing.
Now acting as NEOL’s scientific advisor, Sergei has dedicated his life’s work to extending the longevity of machinery, preserving natural resources, and reducing our impact on the environment. This has been achieved through decades of research into tribology (the study of friction, lubrication, and wear) and the subsequent creation of a groundbreaking copper-filming technology called CuGlide.
In this interview – part two of our interview series – we delve into Sergei’s journey; discussing chance encounters, breakthrough discoveries, and the difficulties of bringing change to an industry stuck in the past.
Q: Hi Sergei. First of all, could you tell us a bit about your background and what fuelled your passion for tribology?
Sergei: Well, at the age of 17, I wanted to be a military pilot. I even applied to flight school. But, when I was directed to helicopter training instead of fighter planes, I quickly followed up with my resignation letter. This led me to my second choice, training as a mechanical engineer at the Russian Institute of Transport (MIIT) with a specialisation in the design of electric locomotives.
It was customary at the time that, following graduation, you spent a few months as an assistant train driver, to help you ‘get to know the rails’. I did, and quickly found out that a lot of work on the railways was being quite poorly run. This prompted me to change direction and, with pilot aspirations still in my head, I started work as an aviation technician. In the process, I found out what real quality in engineering looked like.
In the nineties, things started to change. Cooperatives and private enterprises began to appear, and I set up my own railway business using the knowledge I’d gained from the factory. We worked on repairing couplers, but, alongside our repairs, we would perform a hard alloy melt on the friction surface – which increased the service life of the coupler tenfold.
It has always astounded me that a small change like this can make a huge difference, and I suppose it was around this point that I started to truly see the effects of tribology in action.
Q: Was it also at this point that you discovered ‘The Wearlessness effect’?
Sergei: No, but it certainly led me to it. I firmly believe that everything happens for a reason, that we are all created with a specific purpose, and that fate will guide people to where they need to be. And I am deeply convinced that my early experience was preparing me for meeting Professor Dmitry Nikolaevich Garkunov in 1993.
He was a Doctor of Science, and the author of “The Wearlessness Effect” (Scientific Discovery #41, USSR, 1964) and “Hydrogen Wear of Metals” (Scientific Discovery #378, USSR, 1967). These discoveries demonstrated the effect hydrogen has on metal and how metal can be selectively transferred during friction – both of which have been instrumental in the creation of CuGlide.
At the time I was driving a small ‘Oka’ car that I’d bought direct from the factory. Yet, after just one year, it was already showing the signs of wear. We made some repairs, changed the engine and rings, but the issues still persisted. Then, one day, my technologist brought me a small bottle of bright green liquid to pour into the engine oil. I did…and the results were lifechanging.
Honestly, the car felt as if it had been replaced by a new model. I was so in awe of the effects of this green additive that I had to find out more. It turns out our technologist happened to be a student of Prof Garkunov, who had produced this additive, and this small encounter led to our meeting. The rest, as they say, is history.
Q: So, it is safe to say this meeting with Prof Garkunov had an impact on your career?
Sergei: It didn’t just impact it, it completely changed it. We quickly became friends and started collaborating on projects; conducting research in institutes, embarking on a massive project to study the causes of rail wear, and producing irrefutable proof of hydrogen wear.
Together, we combined his two scientific discoveries into one process. While Garkunov and his followers had been studying both hydrogen wear and selective metal transfer, they had been studying them as two separate phenomena. I was the first to bring them together; hydrogen wear and preparation of the friction surface first, followed by the transfer of copper ions to form a thin, protective layer.
This led to some incredible results. We were producing lubricants that reduced rail and wheel wear by around five times, reduced component failures by up to 20 times, and led to fuel savings of between 15-20%.
Essentially, we had developed an alternative approach to lubrication that not only saved money, but greatly reduced machine waste and fuel consumption as well.
Q: Were these discoveries well received at the time?
Sergei: In short, no. It was actually quite the opposite. We were challenging an approach that had been the standard for years, presenting an alternative that would significantly reduce production and consumption – which was a major disadvantage for suppliers, manufacturing companies and marketers.
We found the tests on railways easy to launch because of our strong connections within the industry, but even there we saw attempts by officials to hide the results of our work. Other industries were equally difficult. We tried at one point to partner with large shipping companies, but there was no route in. That said, we managed to work with a private captain who owned a small 200-ton vessel, and found that our oil was saving him roughly one tonne of diesel fuel per day.
Eventually, we created the company CUPPER. Like many startups we had a building the size of a garage and very basic equipment, producing oils and lubricants in a small reactor. But our technology was getting the results, and we found it was welcomed in areas where performance was more important than money. Sports became a focus, with our oils being used across car racing, motor sports and water sports.
Later down the line we met Dmitry and Leyla, who were central to the growth of CUPPER. They helped to establish our own laboratory, expanded our testing capabilities, grew our team, and together we found new directions to explore. But still, despite the expansion, our technology had much more to deliver.
Q: And this is when NEOL was formed? To present your technology in front of a global audience?
Sergei: Yes, of course. We’d spent decades researching, developing, and refining CuGlide technology to get it to the point it was ready to share. Now NEOL is on the market, with a non-toxic, no-SAPS additive than increases fuel economy, improves machine performance, and at the same time eliminates wear almost in its entirety. That means less money spent, less waste created, and less CO2 released into the atmosphere.
We are in a period of time in which businesses are facing the dual challenge of reducing costs while meeting tightening eco-targets, which is exactly what we offer. And, once CuGlide gains traction, the potential impact it can have on the world is monumental.
In the meantime, we will continue testing and developing our technology. We are, in fact, running tests right now across China and the UK to further demonstrate its effects on different engines.
Q: Excited to see those results! Final question, what does the future look like for NEOL Technology?
Sergei: Our work has been directed at finding a solution to wear and extending the longevity of machines. Now, I personally believe our formula is close to perfection, but we still can’t stop here. Our technology will continue to grow and evolve, even after we are all gone, and will become a long-lasting story for the benefit of humanity.
In the more immediate future, however, our research will be focused on improving lubricants for the gearboxes of electric drives – those used in electric vehicles (EVs) and wind turbines. There is a lot of work still to get EVs to the point that they are commercially and economically viable, and we believe that improving the maximum service life of the mechanisms within them can make a massive difference.
And, of course, we will continue spreading the knowledge of CuGlide technology with the world.